Exclusive Analysis
The Development of the Battery Raw Materials Market
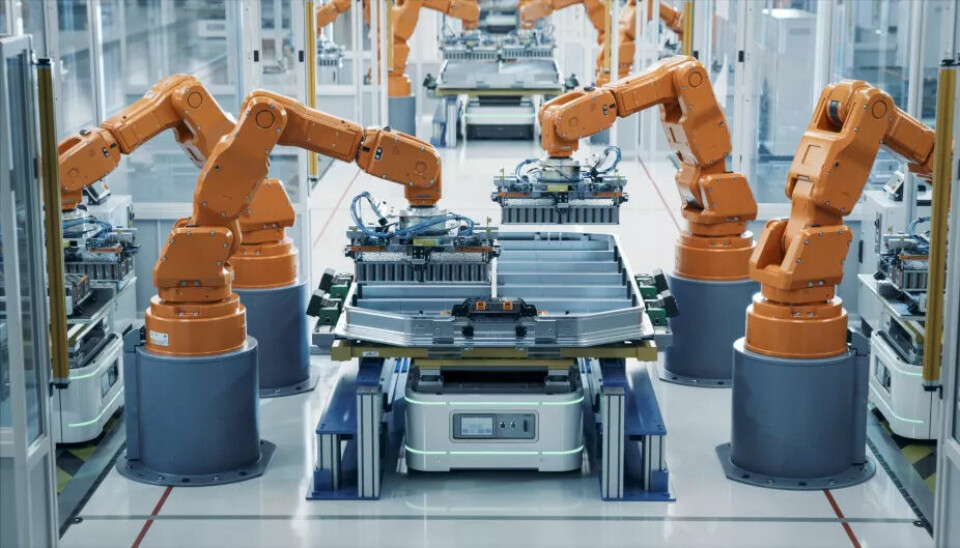
The European industry remains too dependent on risky imports from abroad for battery materials. This is shown by a recent analysis, which is exclusively available to Automobil Produktion.
Customers have high expectations for electric vehicles: They want the electric cars to enter the market with as much range as possible and at a low price. Additionally, buyers and regulators expect ethical standards in the supply chain. This is a challenge for manufacturers - after all, about a third of the vehicle costs are attributed to the battery. To keep production costs low, many manufacturers rely on the cheapest possible raw materials, making them dependent on exports from countries like the Congo (cobalt) or China (graphite). Experts from Berylls Strategy Advisors, together with researchers from the Fraunhofer Research Institution for Battery Cell Production FFB, have examined the exact situation in the global market for battery raw materials in a study, the results of which are exclusively available to Automobil Produktion.
LFP technology could become a success model
In the production of cathode materials for batteries, lithium-nickel-manganese-cobalt oxides (NMC) and lithium iron phosphate (LFP) currently dominate the world market. According to the study, there is a trend where volume manufacturers focus more on LFP batteries, while premium manufacturers concentrate on NMC batteries. The reason for this is the lower price of LFP technology or the higher performance of NMC batteries. The cathodes used account for about 60 percent of the total cost of battery cells in NMC batteries and about 25 percent in LFP batteries. This is mainly due to the price of the required materials lithium, nickel, and cobalt.
Comparison Values for LFP and NMC Batteries
However, there is movement in the market: According to the study authors, the prices for battery materials have significantly decreased over the past year: Nickel has become about 29 percent cheaper, and the price of cobalt has fallen by 16 percent. When purchasing lithium, costs are even 56 percent lower. The reason for this is the high production volume in a simultaneously stagnating market for electric vehicles, which has disrupted the balance of supply and demand, according to the analysts. Particularly for lithium, analysts at J.P. Morgan expect in their own study that the oversupply will persist for another three to four years. However, from around 2027, rising prices for critical materials are expected again.
The study authors consider the production costs for batteries as a key lever for reducing the resulting costs. Through the increasing efficiency of relevant machines and systems or the reduction of waste, cost savings of around 30 percent can be expected by the year 2035. Further possibilities could arise through new construction methods, such as within the framework of cell-to-pack or cell-to-chassis models, which could make battery modules redundant.
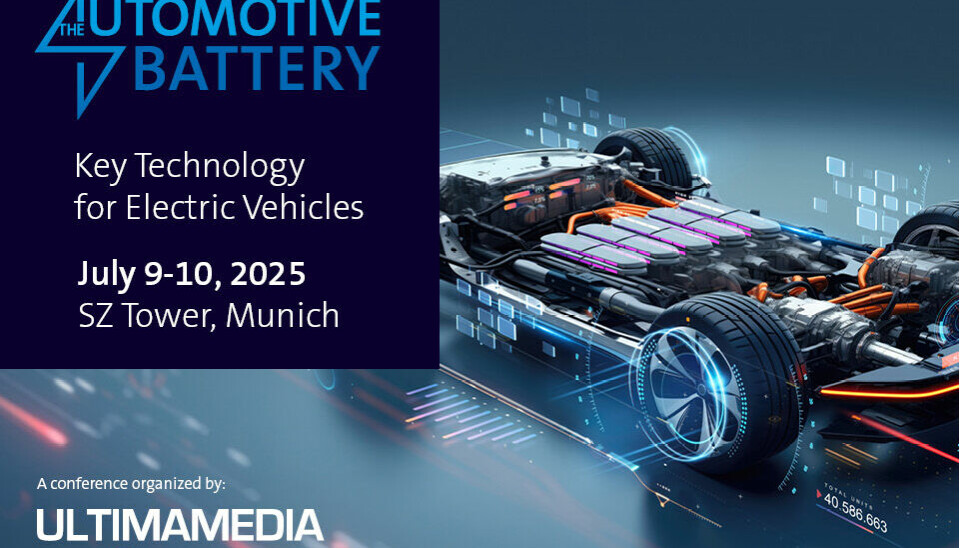
Supply chains for battery materials are vulnerable
Apart from material costs, analysts identify two major challenges in the future value chain for batteries: the resilience of supply chains and new regulations. The first group includes political factors such as trade barriers or sanctions, risks around the mines themselves (such as strikes, lack of labour or natural disasters) and their operating companies (such as insolvencies, sanctions or acquisitions). In the ESG area, possible risk factors are primarily violations of labour law or the impact on the environment. The situation is increasingly exacerbated by the strong localisation of individual raw materials: while around 48 per cent of lithium currently comes from Australia, around half of global nickel production comes from Indonesia. Global cobalt production even takes place 74 per cent in the Congo. In the case of lithium, the authors already point to existing initiatives by car manufacturers to bring raw materials closer to their own sphere of influence, but in the case of nickel and cobalt, this is more difficult.
Manufacturers are working on localisation and tracing
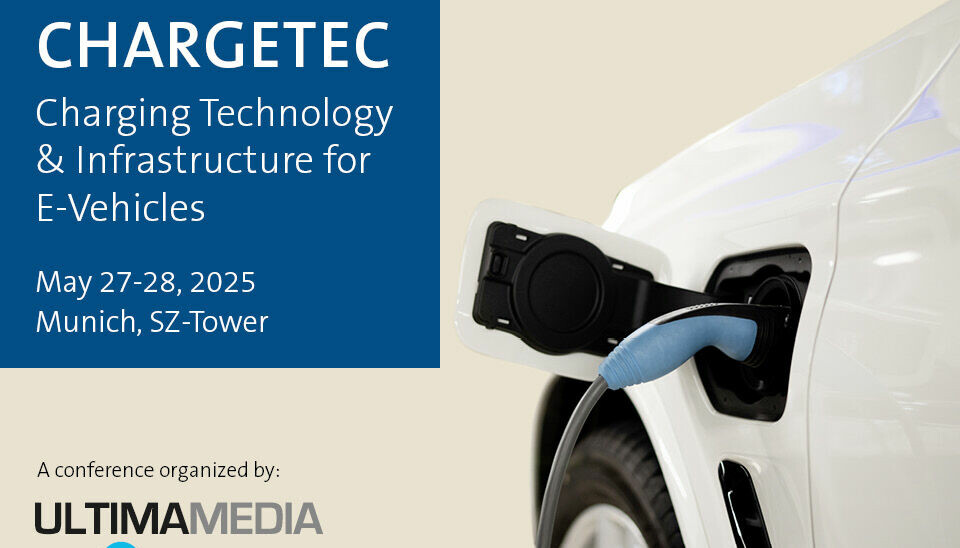
To ensure the security of supply chains, several trends in car manufacturers' strategies are currently being observed, according to analysts from Berylls and Fraunhofer: On the one hand, most of the car manufacturers considered (such as BMW, Volkswagen and Tesla) rely on their own procurement of raw materials instead of trusting cell manufacturers. This increases traceability within the supply chain, among other things. Furthermore, there is a tendency towards localisation. This affects the areas of mining, refining, manufacturing and recycling equally, with the aim of building appropriate circular economy systems. All car manufacturers equally emphasise the high relevance of recycling processes as a future supplier of raw materials. However, the analysts emphasise that the success of corresponding strategies could only be achieved in the long term. Finally, it can be observed that many car companies rely on acquisitions, investments, insourcing or joint ventures to strengthen their own position.
New technologies improve the balance of batteries
Due to regulatory pressures alone, it is expected that the automotive industry will continue on the path to sustainable sourcing of raw materials in the future. However, a greater boost will be experienced through technological innovations. On the one hand, there is expected to be a stronger market penetration of LFP cells, which do not require nickel and cobalt and whose energy density is expected to reach the level of NMC cells in the future. But also in the further development of NMC cells, a lower cobalt content can be assumed. New energy storage systems such as sodium-ion batteries could also ease the raw material issue in the future. Other game changers include new mining methods such as Direct Lithium Extraction (DLE), where lithium could be extracted directly from rock without the detour via evaporation ponds, as well as the future higher degree of recycling materials. In particular, through the recycling of materials, it is possible to localise the raw material cycle more strongly and thus achieve both more sustainability and more security in one's own supply chains.
This article was first published at automotive.eu